1. chipless forming of stabilizers for electromechanical anti-roll bars with GFU Maschinenbau GmbH
Tubular stabilizers, often referred to as “tubular stabilizers”, are essential components in modern mid- and luxury-class cars. They play a key role in the driving stability and handling of vehicles, especially in reducing rolling movements in bends or on uneven roads. Active roll stabilization systems, in which tubular stabilizers often act in combination with gearboxes or servomotors, significantly improve both ride comfort and dynamic performance.
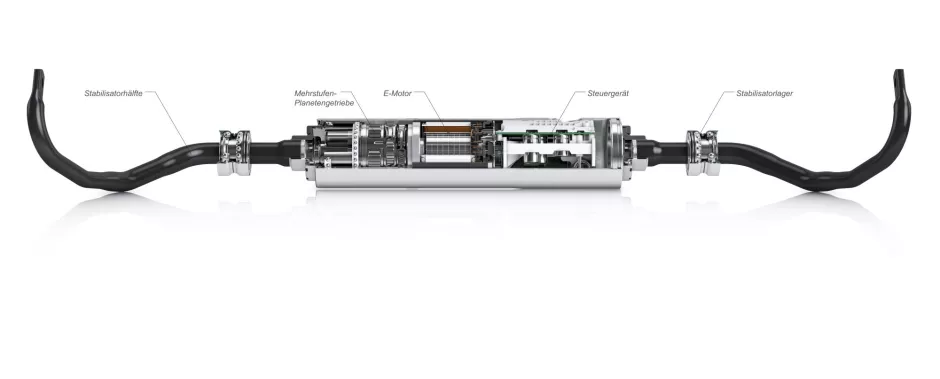
In such systems, sensors constantly monitor the driving conditions. When cornering or changing direction, forces are exerted on the stabilizers to maintain vehicle balance and minimize roll. This is particularly important in the mid and luxury class, where a balance between sporty handling and a high level of comfort is required.